DMLS POSTUPAK
DMLS (engl. Direct Metal Laser Sintering) je prva komercijalna metoda aditivne proizvodnje metalnih dijelova iz praha. DMLS postupak omogućuje izradu proizvoda kompleksne geometrije, s kanalima promjenjivih tokova i različitih presjeka.
Princip rada DMLS proizvodnog postupka je sljedeći: polazni materijal je metalni prah, a izvor energije za srašćivanje čestica praha laser.
Komora za gradnju puni se inertnim plinom (npr. argonom) kako bi se smanjila oksidacija metalnog praha, a zatim se zagrijava na optimalnu temperaturu gradnje.
Na platformu za gradnju nanosi se tanki sloj metalnog praha preko kojeg se prolazi laserskom zrakom. Zbog velike snage lasera dolazi do sinteriranja, tj. toplinskog srašćivanja sitnozrnatog materijala. Nakon završetka sloja, radna ploha na kojoj se obavlja postupak ispisa spušta se za iznos debljine jednog sloja. Na radnu plohu nanosi se novi sloj praha koji se izravnava pomoću translatornog noža. Translatorno gibanje noža gura neiskorišteni prah preko platforme. Po novom sloju praha ponovno prolazi laserska zraka. Svaki prolaz snopa preklapa se s prethodnim i ponovno topi sloj ispod, spajajući metal u homogenu masu i formirajući slojeve. Postupak nanošenja i srašćivanja praha sloj po sloj se ponavlja sve dok nije izrađen kompletni dio, slika 1.
Debljina sloja najčešće iznosi između 0,075 do 0,1 mm te ovisi o propisanim specifikacijama printera, vrsti materijala i funkciji proizvoda.
Kada je postupak izrade gotov, dijelovi su u potpunosti pokriveni metalnim prahom. Gotove proizvode potrebno je postupno ohladiti prije vađenja iz printera. Svi dijelovi proizvoda moraju se ravnomjerno ohladiti kako bi se mogli izlagati sobnoj temperaturi. Ako su dijelovi i/ili praškasti sloj prerano izloženi sobnoj temperaturi, prah se može razgraditi u prisutnosti kisika, a dijelovi deformirati zbog neravnomjerne termičke kontrakcije. Vrijeme hlađenja ovisi o veličini i geometrijskoj kompleksnosti izrađenog modela. Nakon hlađenja, izrađeni proizvod se pažljivo uklanja s radne plohe na koju je spojen potpornim materijalom, čisti se od viška praha te se po potrebi šalje na dodatnu obradu. Dijelovi se najčešće uklanjaju s platforme rezanjem ili strojnom obradom. Nakon svakog postupka ispisa, neiskorišteni prah se sakuplja i prosijava te mu se dodaje novi, svježi prah. Na taj način stvara se manje otpada te se povećava iskoristivost sirovog materijala.

Karakteristike EOS M 290 printera
Za potrebe izrade čepova korišten je printer EOS M 290 koji ima procesnu komoru radnog volumena 250 x 250 x 325 mm. U komori se nalazi podizni sustav i sustav za grijanje, optički sustav s laserom, sustav za upravljanje procesnim plinom, računalo kojim se kontrolira proces te skup standardne opreme (oprema za čišćenje, osnovni alati za pokretanje i uklanjanje dijelova, sustav za hlađenje), slika 2. Printer EOS M 290 omogućuje izradu proizvoda složene geometrije, uključujući elemente površine slobodnog oblika, duboke proreze ili kanale za rashladno sredstvo. Polazni materijali su metalni prahovi legure aluminija i titana, alatni čelik, kobalt krom legure, nehrđajući čelik te plemeniti metali. Promjer laserske zrake iznosi 0,1 mm, jačina laserske zrake 400 W, dok procesni plin može biti argon ili dušik. Najtanja debljina sloja koja se može izraditi iznosi 20 µm, a ovisi o vrsti materijala.
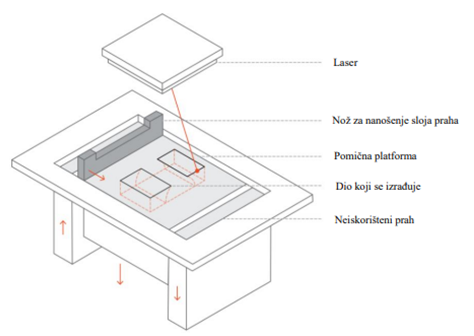
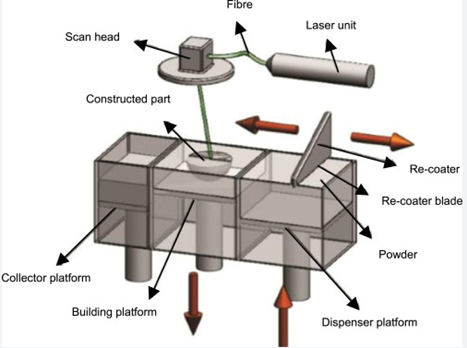
Metal u praškastom obliku prikazan je na slici 3. Prah se najčešće dobiva postupkom raspršivanja, što uključuje atomizaciju materijala plinom, vodom, vakuumskom indukcijom ili centrifugom. Raspršivanje pomoću plina jedan je najčešćih postupaka za dobivanje praha, a djeluje tako da se rastaljeni metal raspršuje neutralnim plinskim mlazom. Prilikom izrade praha može doći do nedostataka poput izduženih čestica, malih zrnca zaglavljenih na površini većih te šupljih čestice koje uzrokuju teži ravnomjerni raspored prilikom nanošenja slojeva, a time i manju kvalitetu gotovog proizvoda. Veličina čestica praha koja se najčešće koristi je između 30 i 40 μm, a česta je interakcija manjih i većih čestica. Manje čestice između većih omogućuju širenje gušćeg sloja praha. Ako su sve čestice iste veličine, to će ostaviti praznine između čestica praha, što će uzrokovati stezanjem gotovog proizvoda. Gustoća praškastog materijala kreće se između 50 i 60%. Što je veća gustoća praha, veća je i toplinska vodljivost sloja i bolja su mehanička svojstva proizvoda. U slučaju pogrešno postavljenih parametara, strategije izrade, orijentacije dijela ili nedovoljne količine praha, dolazi do određenih nedostataka poput nerastopljenih čestica praha, pora, pukotina, uključaka, zaostalih naprezanja ili slabe površinske hrapavosti.
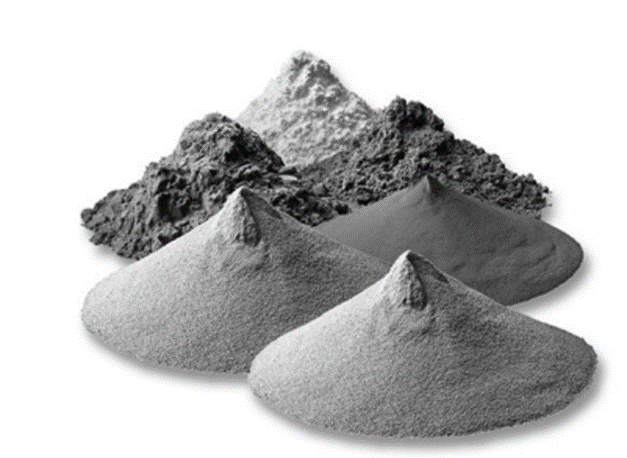
Legura AlSi10Mg
Legura AlSi10Mg je poznata, konvencionalno lijevana Al-Si legura, koja je široko korištena zbog izvrsne zavarljivosti i izvrsne livljivosti. Nadalje, poznato je da ova legura ima brojne prednosti; uključujući visok omjer čvrstoće i gustoće, dobru otpornost na habanje, dobar koeficijent toplinske ekspanzije, poboljšanu otpornost na koroziju i dobra mehanička svojstva, te je stoga najraširenija aditivno proizvedena i komercijalizirana Al legura. Također, DMSL postupak izrade AlSi10Mg dijelova nudi značajne prednosti u odnosu na tradicionalne proizvodne procese. Nema geometrijskog ograničenja što se tiče kompleksnosti dijelova, moguća je izrada personaliziranih dijelova, gotovo da nema potrebe za naknadnom obradom, skraćuje se vrijeme izlaska na tržište proizvoda, visoka je razina fleksibilnosti, dok su sva svojstva i kvaliteta proizvoda usporedivi su s konvencionalno izrađenim dijelovima ili čak poboljšani.
Zbog navedenih karakteristika, spomenuta aluminijska legura najčešće se koristi u zrakoplovnoj i automobilskoj industriji za izradu dijelova podvrgnutih velikim opterećenjima gdje je potrebna kombinacija dobrih mehaničkih i toplinskih svojstava. Veličina čestica praha iznosi 30 ili 60 µm. Zbog izgradnje u slojevima, dijelovi imaju anizotropna svojstva. Toplinskom obradom mogu se poboljšati mehanička svojstva proizvoda te umanjiti anizotropnost svojstava.
Tekst je pripremila dr.sc. Ivana Mihalic Pokopec, mag. ing.mech., Voditeljica odjela za tehnologiju u Metalskoj jezgri Čakovec – odgovorna za provođenje znanstveno-istraživačke djelatnosti, s naglaskom na stvaranje novog intelektualnog vlasništva te na primjenu rezultata istraživanja na korisnike iz industrije, odnosno na tržište u vidu komercijalizacije proizvoda i usluga.